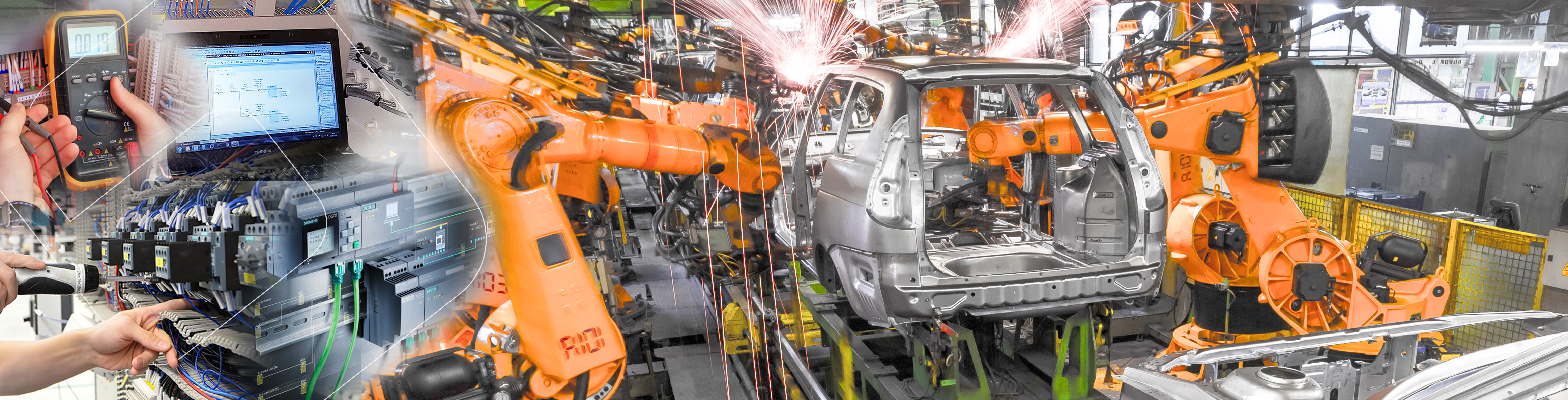
Implementation
Normally, after the engineering and design phase of each project, normally implementation would be the next phase, typically in the APQ for the implementation of each industrial automation project following 4 stages are considered:
1- Control Engineering & Programming
Following project design phase, it’s time to start developing the programming and physical control panels required for your system. Broad categories of programming include:
- DCS Programming
- Logic Programming
- PC-Based Programming
- PLC Programming
- Operator Interface Programming
Often, this step involves EPIC strategically designing programming based on information from line-operators to upper management to understand how people at various levels will interact with our final solution. A fancy automation system with a million options and hard to navigate interface doesn’t help plant operators run a line or upper management plan resources.
Engineers of APQ want their solutions to stand out not for their complexity, but for their fit to everyday practical applications, smooth startup, and longevity.
2- Fabrication, Testing
With the project planned, system designed and programming set up, you’ll need a panel fabrication and assembly team to build various system components. We handle this in-house and the same project manager developing your controls oversees:
- Control cabinets
- Hardware
- Wiring
All automation hardware is fully built and tested for the proper area classification, GMP standards, and client specific standards. Our state-of-the-art fabrication shop offers a controlled environment, expert craftsmen, and a dedicated quality assurance team.
3- Installation
The onsite installation process entails:
- Installing any pre-fabricated and tested control panels
- Installing all programming and software upgrades
- Linking in-feed and out-feed equipment
- Adjusting power distribution and making site modifications as required
- Integrating new controls with existing plant systems (for proper communication)
The key to installation is to keep downtime to a minimum —every hour of downtime costs thousands or even tens of thousands depending on the plant. APQ will Coordinate the installation with your responsible people to minimally impact your existing operations, and will ensure that pre-tests of all automation equipment before shipment to deliver a rapid startup has been done.
4- Startup & Integration
The last phase by APQ is to ensure all systems are:
- Fully installed
- Functioning properly
- Successfully handed off to your team
APQ automation department provide you with a comprehensive handoff, complete with:
- Operations manuals
- Staff training on how to use your new systems
- Recommended spare parts lists
- Full documentation
- Continuing support post-handoff