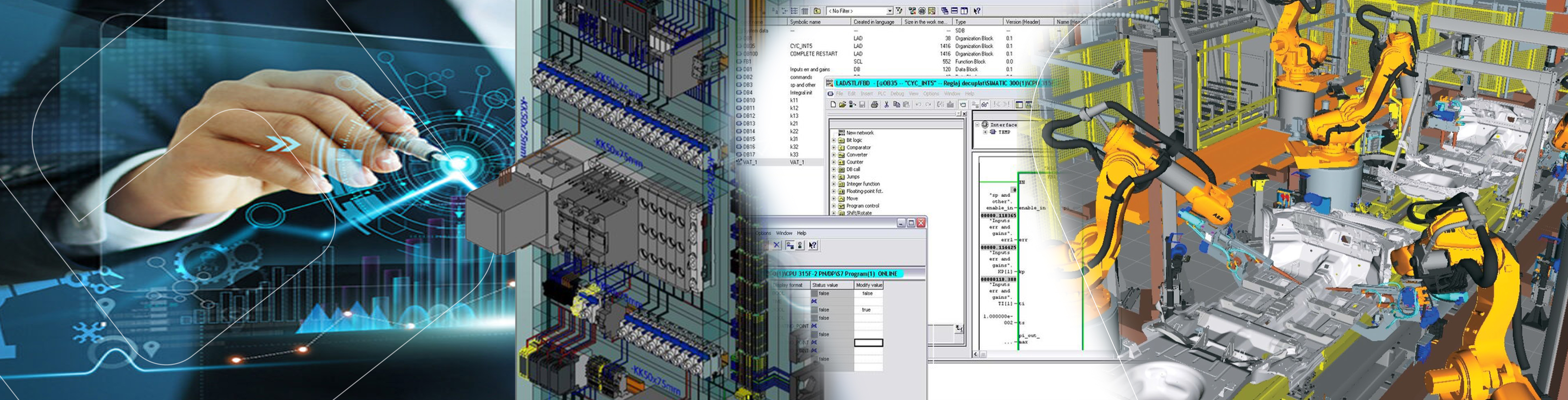
Engineering
Automation Engineering
Engineering is one of the fields that has many enthusiasts, however, you should know that this field has several different trends and sub-fields. One of them is automation engineering, which is to integrate standard engineering fields. Automatic control of a variety of control systems for the operation of various systems or machines to reduce human effort and time to increase accuracy. An automation engineer must have an understanding of the systems, networks, hardware, and software that he or she works with. Required programming languages are C #, SQL and Java; However, the programming languages and tools required vary from industry to industry. The software used for automation engineering is automated test software. These tools can also be useful in solving automation problems, reporting, and automating the Q&A test process. Stay tuned to asampaivar for more.
What is Automation Engineering?
The word automation means dictation or a mechanism that moves by itself. Generally the Greek words Auto and Matos are derived where auto means self while Matos means movement. Automation has gone one step further than mechanization, which uses a special machine mechanism that helps human operators to do a job. Manual operation mechanization is a task using powerful machines that depends on human decision making. On the other hand, automation uses logical programming commands and powerful machines to replace human intervention. In short, industrial automation can be defined as the use of automated technologies and automated control devices that lead to the automatic operation and control of industrial processes without significant human intervention and achieve superior performance over manual control. These automation devices include PLC, PC, PAC, etc., and technologies include a variety of industrial communication systems.
What is automation?
In general, automation is the use of control systems (numerical control, programmable logic control, and other industrial control systems), mechanical, electronic and computers [CAM, CAD, CAX] to monitor (control) the production line, which aims to That; Reduce the need for manpower. Automation is the connection of information components of different parts of an organization in the form of a platform to transfer information, statistics and instructions in a fully integrated and easy way, so that the exchange, adjustment and correction of information within the organization is accelerated. Accept. Another name for automation can be called robotization, which means the use of control tools (such as computers) to guide and control industrial machinery and production processes.
Automation or mechanization?
Automation has eliminated the human role in the process and replaced it with logical programming and intelligent devices. In industrial automation, computers and machines will think and make decisions instead of humans. Mechanization means providing human operators with tools and devices that help them do their job better. The most well-known part of automation (mechanization) are industrial robots. Automation is a step beyond mechanization. Mechanization uses a set of mechanical equipment that will need human help to perform the desired activity.
Benefits of automation
- increasing production
- Doing things that are beyond human ability, such as carrying very heavy loads, very large objects, too hot or too cold, or materials needed for things too fast or too slow.
- Improving the economy: Sometimes and some types of automation, improves the economics of organizations, society, and many people.
- Remote monitoring assistance
- Reproducibility of activities and processes
- Increasing the power and efficiency of industrial units
- Reduce operator costs
- Fix the problem of lack of specialized personnel
- Reduction of waste or production waste
- More precise quality control
- Transfer of labor to service jobs
- Reduction of temporary warehouses
- Improve interaction with business systems
Disadvantages of automation
- Reduce labor force and increase unemployment
- High initial costs of implementing automation
Hierarchy of an industrial automation system
All industrial automation systems can be very complex in nature because they have a large number of devices that work with automation technologies. The following figure describes the hierarchical arrangement of the automation system consisting of different hierarchical levels.
1. Square level
This is the lowest level of the automation hierarchy, which includes field devices such as sensors and actuators. The main task of these field devices is to transfer process and machine data to the next higher level for monitoring and analysis. It also includes controlling the process parameter through stimuli. Stimulators convert electrical signals (from controllers) into mechanical tools to control processes. Flow control valves, solenoid valves, pneumatic actuators, relays, DC motors and servo motors are examples of actuators. Sensors convert real-time parameters such as temperature, pressure, current, surface, etc. into electrical signals. This sensor data is further transmitted to the controller to monitor and analyze real-time parameters. Some sensors include thermocouple, proximity sensor, RTD, flowmeter.
2.Control level
This level includes various automation machines such as CNC machines, PLCs, etc. that receive process parameters from various sensors. It consists of various modules such as CPU, analog I / O, digital I / O and communication modules. This allows the operator to schedule a control function or strategy to perform specific automated operations in the process. Automatic controllers drive actuators based on processed sensor signals and control program or technique. Programmable Logic Controllers (PLCs) are the most widely used powerful industrial controllers that are capable of delivering automatic control functions based on sensor input.
3. Level of production supervision and control
At this level, the Distribution Control System (DCS) or SCADA is mainly used. At this level, automated devices and monitoring systems facilitate control and intervention functions such as human machine interface (HMI), monitoring of various parameters, setting production targets, historical archiving, setting up and shutting down the machine, and so on.
4. Information or organizational level
This is the highest level of industrial automation that manages the entire automation system. Tasks at this level include production planning, customer and market analysis, orders and sales, etc., so it focuses more on business activities and less on technical aspects. From the hierarchy it can be concluded that there is a continuous flow of information from the top level to the bottom level and vice versa. If we assume this graphic form, it is like a pyramid in which information is aggregated as it ascends, and as we descend, we obtain accurate information about the process. Automation Engineering The goal of an automation engineer is to eliminate product deficiencies and issues or develop software related to business processes or customer service processes. Industrial communication networks are more prominent in industrial automation systems that transfer information from one level to another. Therefore, they exist at all levels of the automation system to provide a continuous flow of information. This communication network can vary from one level to another. Some of these networks are RS485, CAN, Device Net, Foundation Field bus, Profibus and ...
What are the advantages of modern automation systems and instrumentation based on PLC?
- Their installation and commissioning costs are low.
- Input connections have standard output and signal levels.
- Their programming language is simple and high level.
- Protected against noise and environmental disturbances.
- Remote control (for example via telephone line or other communication networks) is possible.
- It is possible to connect many standard peripherals such as printers, barcode readers and… to PLCs.
- It is easy to change the program while working
- They take less time to install and set up.
- They are small in physical size.
- They are very easy to maintain.
- Easily expandable.
- Ability to perform complex operations.
- Have a high degree of reliability in the implementation of control processes.
- They have a modular structure that simplifies the replacement of different parts.
- It is possible to create a network between several PLCs easily.
Index tools in automation
The truth is that automation has nothing to offer, and in fact, by bringing together some tools and creating a lively and effective connection between them, we can see a fully professional automation, these key tools are;
- ANN artificial neural network
- Instrumentation
- Motion control
- robotic
- HMI human-machine interface
- DCS Distributed Control System
- SCADA Supervision control systems and data collection
- PLC programmable logic controller
- Programmable PAC automatic controller
- machine vision & image processing systems based on machine vision and image processing.
Some automation performance
Increase Productivity
By using automation in production lines and with better and more precise control over the process, the production rate can be significantly improved. In fact, the time spent per production of each product will be reduced, along with the quality and accuracy of the production of goods will increase.
Reduce production costs
Combining different processes in the industry using automation, as mentioned in the previous section, will reduce production time; Along with this reduction, the need to use humans during the process also diminishes. Therefore, the costs of producing goods will thus be significantly reduced.
Increase the quality of goods
Since the use of automation will reduce human interference in the process, the possibility of human error will also be minimized. In this way, the goods produced will have a much better quality than before, using the operation of automation equipment and careful inspection and control of them from the design to construction stage.
Increase security
By replacing industrial machines with humans, industrial automation will prevent human presence in hazardous environments and thus increase workplace safety.
Types of processes in automation
Discrete: It has a high degree of flexibility so that several completely different work shifts can be implemented in one workshop, factory, production unit, etc. in one day. Such as cars, electronics, home appliances.
Continuous: Like discrete but less efficient. The production line of the continuous model is completely dedicated to a specific product and it is practically impossible to separate or separate it. Such as refining, petrochemical, chemical, food.
The most important function of automation engineering
- View the current status of each machine and device
- Change and modify Set Points during the production process
- Ability to change some control processes through the monitoring program
- Record information and parameters desired by managers such as operating times, production rate, amount of raw materials consumed, amount of energy consumed and…
- Display and record important and vital parameters of a system
- Display and record various alarms at system error times
- Display the location of the failure and the time of occurrence of the problem in each component of the system
- Display production processes using appropriate graphical tools.